A(M)Cademy of VIBROdiagnostics
#11 Jaka wibrodiagnostyka?
Jaka wibrodiagnostyka?
W tym wpisie chcielibyśmy przedstawić szerszą perspektywę zastosowania różnych systemów, które wykorzystują pomiar drgań mechanicznych. Systemy takie spełniają różne funkcje, a ponadto są przeznaczone do różnych maszyn. Bardzo ważne jest dopasowanie systemu monitorowania do maszyny. Dzięki temu możemy z jednej strony – uniknąć wydatków na zbyt zaawansowany system, a z drugiej – uniknąć przesadnej oszczędności, jeżeli zdecydujemy się na rozwiązanie, które nie zapewni podstawowych funkcji potrzebnych do utrzymania ruchu rozważanej maszyny. W najgorszym przypadku wadliwie wybrany system nie będzie w stanie wykryć jej uszkodzeń.
Co mierzyć?
Przede wszystkim należy pamiętać, że systemy oparte na pomiarze „drgań” tak długo pomogą nam utrzymać maszynę w dobrym stanie technicznym, jak długo uszkodzenia będą generować przede wszystkim dodatkowe „drgania” – a to założenie, choć atrakcyjne, nie zawsze jest prawdą. Zatem warto rozpocząć przygodę z klasyczną wibrodiagnostyką od poznania tego szerszego tła, czyli od pozostałych rodzajów pomiarów (pomiar temperatury, analiza modalna, pomiar naprężeń, pomiary elektryczne, pomiary składu oleju, pomiar hałasu, etc.). Często okazuje się bowiem, że dla danego obiektu, istnieje ten najprostszy i najefektywniejszy sposób oceny stanu technicznego, pasujący do warunków eksploatacyjnych.
Zadania systemów opartych na pomiarze drgań
Jeśli już decydujemy się na pomiar drgań, w kolejnym kroku odpowiadamy na pytanie – czego oczekujemy od systemu? W przypadku ogólnej rodziny systemów monitorowania i diagnostyki maszyn, pytanie to odpowiada bardziej skonkretyzowanym zadaniom systemów, co przestawiono w Tabeli 1.
Tabela 1 Zadania systemów monitorowania
Zadanie systemu | Pytanie | Cechy systemu |
Detekcja uszkodzenia | Czy jest uszkodzenie? (TAK/NIE)ISO 20816 | Wskaźniki szerokopasmowe |
Identyfikacja uszkodzenia (element mechaniczny) | Który element mechaniczny jest uszkodzony? | Model kinetostatyczny + wskaźniki wąskopasmowe |
Identyfikacja uszkodzenia (rodzaj uszkodzenia) | Rodzaj uszkodzenia (niewyrównoważenie, BPFO, etc.) | Analiza widmowa |
Poziom istotności uszkodzenia (ewaluacja) | Jak poważne jest uszkodzenie | Analiza trendów |
Prognozowanie | Jak długo maszyna może jeszcze pracować bez awarii? | Progi alarmowe, modelowanie (mat. aproksymacja punktowa) |
RCA (Root Cause Analysis) | Jaka jest pierwotna przyczyna uszkodzenia? | Zaawansowana analiza danych historycznych, warunków eksploatacyjnych + inżynieria materiałów |
Zalecenia (Prescription) | Jakie są dalsze instrukcje dla służb utrzymania ruchu? | Nowoczesne moduły (w fazie rozwoju) |
Królową detekcji uszkodzenia jest estymata VRMS (zob. post #2), gdyż norma ISO 20816 podaje konkretne, dopuszczalne zakresy wartości skutecznej prędkości drgań w zależności od mocy maszyny i kilku innych parametrów. Identyfikacja może mieć wiele znaczeń, ale w wibrodiagnostyce najczęściej dotyczy szczegółów fizycznych uszkodzenia – w pierwszej kolejności może informować o tym, która część maszyny może być uszkodzona, a następnie jakiego rodzaju to jest uszkodzenie (np. pęknięcie zęba czy uszkodzenie bieżni zewnętrznej łożyska – BPFO). W tym miejscu należy zwrócić szczególną uwagę, że praktyczna implementacja systemów wyróżnia:
- systemy przetwarzające dane bez pomiary znacznika fazy (chwilowej prędkości obrotowej),
- systemy przetwarzające dane z sygnałem znacznika fazy, tj. wykonujące przetwarzania i analizę w dziedzinie rzędów.
Systemy bez znacznika fazy są tańsze i prostsze, ale umożliwiają wyłącznie identyfikację komponentów w niskich częstotliwościach (z uwagi na rozmycie widma). Z kolei systemy ze znacznikiem fazy są droższe, trudniejsze w konfiguracji i montażu, ale za to są znacznie skuteczniejsze w identyfikacji.
Określenie poziomu istotności uszkodzenia (ewaluacja) z reguły wymaga rejestracji historycznej wskaźników diagnostycznych, czyli tzw. trendów (zob. post #3). Klasycznym przykładem tego rodzaju jest wzrost amplitudy wstęg bocznych częstotliwości zazębiania przekładni (zob. post #6_1 i 6_2). Dalsze zadania diagnostyki – tj. prognozowanie, RCA (z ang. Root-Cause-Analysis) oraz zalecenia (oryginalnie z ang. Prescriptions) w praktyce wciąż pozostają w fazie rozwoju, z uwagi na problemy związane m.in. z parametryzacją metod, przetwarzaniem wstępnym oraz wyborem cech diagnostycznych.
Rodzaje systemów „monitorowania”
W żargonie inżynierskim często mówimy ogólnie o systemie „monitorowania” mając na myśli system „monitorowania i diagnostyki”. Jednocześnie, mówimy o analizie „diagnostycznej”, jako o procesie analizy danych. Co ciekawe, w literaturze często operujemy często angielskim skrótem CMS, co oznacza „Condition Monitoring Systems”, a więc tłumaczenie nazw nie jest literalne.
W praktyce, rodzaje systemów przejrzyście dzielą się na systemy zabezpieczeń, systemy monitorowania oraz systemy diagnostyki. Wszystkie systemy mogą występować rozłącznie, ale mogą być też łączone w różnych konfiguracjach zarówno na poziomie sprzętowym, jak i aplikacji. Rys. 1 przedstawia mapowanie rodzajów systemów opartych na pomiarze drgań na zadania tych systemów opisanych w poprzednim punkcie.
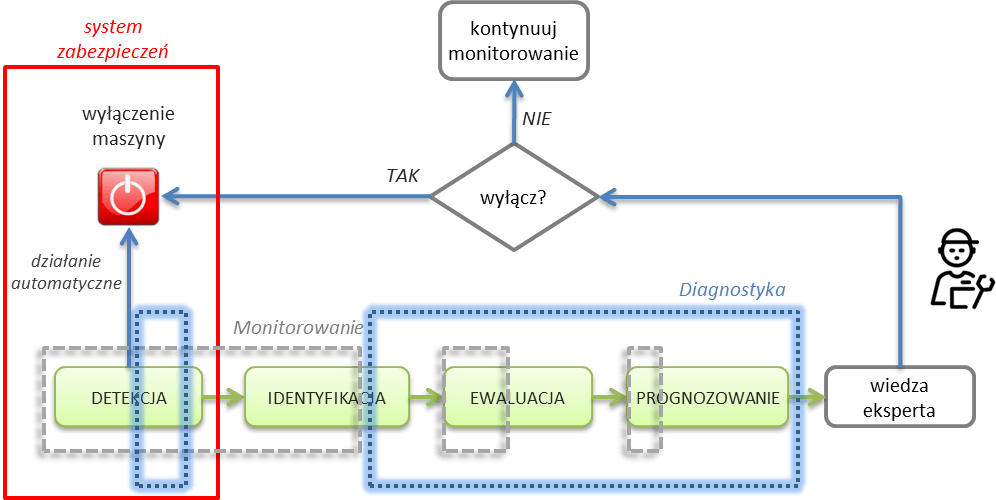
Rysunek 1 Rodzaje systemów opartych na drganiach rzutowane na zadania
Jak pokazano na Rys. 1, systemy zabezpieczeń na podstawie zdefiniowanych analiz automatycznie może wyłączyć maszynę. Takie systemy są różne od systemów monitorowania opisanych w postach, gdyż są to z reguły systemy przetwarzające drgania względne (pomiar odległości, a nie przyspieszenia drgań) i są spotykane głównie w elektrowniach w ramach oceny stanu technicznego turbogeneratorów. Niemniej jednak, istnieją również systemy zabezpieczeń oparte na pomiarze drgań – w tym wypadku śledzone są z reguły wartości szerokopasmowe (zob. post #2).
Systemy monitorowania – to w skrócie systemy zawierające „moduł trendów i moduł zdarzeń”. Moduł trendów umożliwia wyświetlanie historycznych wartości wskaźników diagnostycznych. Moduł zdarzeń odpowiada za proces, który porównuje wartości bieżące wskaźników z dopuszczalnymi progami i generuje zdarzenie (mail/sms, lampka, dźwięk, piktogram, etc.) w przypadku przekroczenia dopuszczalnego progu (zob. post #10). Jak widać na Rys. 1, monitorowanie dotyczy detekcji oraz częściowo identyfikacji (pełna identyfikacja wymagałaby 100% skuteczności w definicji analiz wąskopasmowych a priori, co jest niezwykle trudne do osiągniecia) oraz częściowo ewaluacji i prognozowania.
System diagnostyki dotyczy w praktyce tego, co oglądamy manualnie – czyli tzw. „figur” (albo wykresów) diagnostycznych. Klasyczne figury (reprezentacje przekształceń sygnałów) to: przebieg czasowy, widmo, widmo w dziedzinie rzędów, widmo obwiedni, widmo w dziedzinie rzędów i wykresy TSA. Dla sygnałów przemieszczeń drgań – jeszcze orbita, wykres linii środka wału, wykres Bode’go, kaskada i pełne widmo. Dodatkowo, `każde widmo może być uśrednione oraz wyskalowane (dotyczy zarówno rodzaju amplitudy – [g], [mm/s^2], moc, RMS oraz skali – liniowa albo logarytmiczna [dB]). Jak pokazano na Rys. 1, analiza diagnostyczna dotyczy części wskaźników szerokopasmowych, części wskaźników wąskopasmowych i analizy trendów tych wskaźników oraz dodatkowo analizy czasowej i widmowej. Ta ostatnia może dotyczyć pojedynczego widma, porównania widma bieżącego z widmami referencyjnymi z przeszłości (reprezentujących stan dobry) oraz wykreślenia kaskady kolejnych widm w czasie. Jednak warto podkreślić, że sama analiza przebiegów czasowych często daje odpowiedź na wiele pytań, a do tego jest nieoceniona w ramach walidacji rejestracji sygnałów.
Wybór systemu monitorowania/systemu zabezpieczeń
Czy zawsze system o większej funkcjonalności lepiej się sprawdzi w przemyśle? – Z pewnością nie. Decyzja o wyborze odpowiedniego systemu jest dość trudna, gdyż trzeba odpowiedzieć na wiele pytań. Z najważniejszych: Czy system ma być przenośny, czy nie? Czy będzie mierzona prędkość obrotowa? Ile kanałów będzie mierzonych? Jaki jest wymagany zakres czujników? Jak długie będą sygnały? Jakie pasmo jest wymagane? Czy dane będą archiwizowane? Jakie figury diagnostyczne są wymagane?, itd. Zarówno zakup systemu o niedostatecznej funkcjonalności, jak i wdrożenie systemu o przesadnej architekturze może spowodować jego finalną niską skuteczność. Dlatego też, rynek systemów CMS jest dość bogaty i stale się rozwija. Poniżej przedstawiono kilka przykładów systemów komercyjnych.
Przykłady systemów monitorowania
Moduł AVM 1000E to jednokanałowe urządzenie, które pozwala na ciągłe monitorowanie i wstępną diagnostykę maszyn wirnikowych, jak wentylatory, pompy, sprężarki itp. Wbudowana linijka (22 punkty) z zaznaczonymi typowymi zakresami ostrzegawczymi i alarmowymi ułatwia określenie stanu maszyny. Wyjście prądowe 4..20mA dla sygnału estymaty (RMS, PEAK) pozwala na bezpośrednie włączenie AVM 1000E do systemu sterowania i nadzorowania monitorowanego urządzenia. Inne wersje serii 1000 posiadają wyświetlacz oraz wyjścia przekaźnikowe. | ![]() |
Moduły serii AVM 2000 występują w różnych wariantach – najbardziej zaawansowany przeprowadza resampling oraz śledzi amplitudę pierwszej i drugiej harmonicznej co pozwala na monitorowanie maszyn o zmiennej prędkości obrotowej oraz maszyn o większych mocach, takich jak: turbiny parowe, turbiny wiatrowe. Do modułu AVM 2115DA można podłączyć czujniki wiroprądowe w celu monitorowania łożysk ślizgowych. Dodatkowo, AVM 2115DA umożliwia zapis wyliczanych estymat/analiz na kartę SD w zdefiniowanych interwałach czasowych. | ![]() |
Moduły z serii AVS 2000R to bezprzewodowe dwukanałowe, w pełni konfigurowalne urządzenia pozwalające na ciągłe monitorowanie i diagnostykę maszyn. Moduł pozwala na przesyłanie informacji na temat stanu maszyn przy pomocy sieci radiowej do systemu, gdzie następuje ich dalsze przetwarzanie. Dane pomiarowe zbierane są cyklicznie zgodnie ze skonfigurowanym interwałem, a w razie problemów z komunikacją przechowywane są w wewnętrznej pamięci urządzenia i przesyłane w momencie nawiązania połączenia tak aby zachowana była ciągłość pomiarowa. | ![]() |
AVM 4000 to modułowy, wielokanałowy i autonomiczny system pracujący przy maszynie. System poprzez kondycjonowanie, wysokiej jakości akwizycję sygnałów i parametrów procesowych oraz ich ciągłą analizę, monitoruje stan oraz zabezpiecza pracę maszyn. Dzięki technologii True Data ValidatorTM, weryfikacji danych w czasie rzeczywistym, automatycznym wykrywaniu stanów maszyny oraz zaawansowanym analizom diagnostycznym system skutecznie identyfikuje anomalie we wczesnym stadium rozwoju oraz zdecydowanie redukuje ilość fałszywych alarmów. | ![]() |
MEGGIT VM600 (MK2) to modułowy system zabezpieczeń przeznaczony do ciągłego monitorowania generatorów w typowych elektrowniach węglowych. Systemy tego rodzaju chronią nie tylko generator, ale również inne urządzenia, dzięki czemu są praktycznie niezbędne w ramach produktywności 24/7. | ![]() |