A(M)Cademy of VIBROdiagnostics
#12 Czujniki bezprzewodowe - moda czy nowy trend?
W ofercie wielu firm pojawiły się bezprzewodowe czujniki drgań. Można znaleźć czujniki bardzo drogie i bardzo tanie, oczywiście zasadniczo różniące się parametrami. Wielu użytkowników systemów monitorowania i diagnostyki zadaje nam pytania, jaka jest wartość tych produktów? Jakie są ich zalety i wady w porównaniu do „normalnych” systemów, które są obecne na rynku od wielu lat. Postaramy się trochę rozjaśnić ten temat.
Podobnie jak klasyczne akcelerometry, bezprzewodowe czujniki drgań najczęściej mierzą sygnał przyspieszenia wykorzystując własności elementów piezoelektrycznych. W skrócie, stosują tę samą konwersję sygnałów fizycznych, tj.:
siła -> prąd -> napięcie -> sygnał przyspieszenia
Pojawiają się też czujniki, które wykorzystują akcelerometry w technologii MEMS, ale zasadnicze cechy obu wariantów są dość podobne.
Od strony użytkowej, stosowanie czujników bezprzewodowych znacznie różni się od stosowania urządzeń klasycznych. Sytuację można porównać do pasażera samolotu, który wybiera się w daleką podróż, ale na lotnisku okazuje się, że z uwagi na zaistniałe ograniczenia, może zabrać ze sobą wyłącznie niewielki bagaż podręczny. Wiadomo, taki bagaż nie pomieści wszystkich rzeczy, które wydają się nam niezbędne, ale zastanówmy się – czy lepiej go mieć ze sobą, czy nie mieć w ogóle? Istota czujników bezprzewodowych jest podobna. Trzeba zdać sobie sprawę jednocześnie z ich ograniczonej funkcjonalności oraz z ich niezastąpionych zalet, aby odpowiednio umiejscowić je w architekturze systemu ciągłego monitorowania. Przykładowe zastosowanie czujników bezprzewodowych przedstawiono na Rysunku 1.

Rysunek 1 Schemat systemu wykorzystującego czujniki bezprzewodowe
Jak pokazano na Rysunku 1, czujniki bezprzewodowe generalnie umieszcza na maszynach pomocniczych, do których w normalnych warunkach nie ma przystępnego dostępu czujnikami przewodowymi. Ponieważ jednym z priorytetów bezprzewodowych czujników drgań jest minimalizacja zużycia energii, dane z tych czujników z reguły nie są bezpośrednio przekazywane do komputera centralnego, ale przechodzą przez jednostkę pośrednią umieszczoną w pobliżu, na Rysunku 1 oznaczoną jako „Gateway” (czyli dokładnie „brama sieciowa”). Jak wskazano na Rysunku 1, pożądaną cechą czujników bezprzewodowych jest możliwość integracji z czujnikami przewodowymi w ramach jednego systemu monitorowania i diagnostyki maszyn CMS (z ang. Condition Monitoring System). Czujniki bezprzewodowe wykonują pomiary dużo rzadziej, więc najczęściej instaluje się je w miejscach, gdzie dotychczas realizowano pomiary sprzętem przenośnym.
Zasięg łączności radiowej
Czujniki bezprzewodowe wykorzystują częstotliwości radiowe do przekazywania informacji. W związku z tym koniecznie należy sprawdzić, jakie są warunki propagacji fal radiowych dla danego otoczenia. Bardzo ważne jest pasmo, w którym pracuje czujnik. Co do zasady, im wyższa częstotliwość fal radiowych, tym większa przepustowość, ale tym mniejszy zasięg. Dla popularnego pasma 868 MHz (którego odpowiednikiem w USA jest pasmo 915 MHz) na otwartej przestrzeni możliwe są osiągi rzędu 1 km, a nawet więcej. Zasięg gwałtownie spada w maszynowni, gdzie mamy ściany i dużo elementów metalowych. Wreszcie, jeżeli maszyna jest zamknięta w metalowej obudowie, czujnik nie może pracować wewnątrz, ponieważ taka obudowa zadziała jak klatka Faraday’a i odetnie łączność.
Zasilanie czujników bezprzewodowych
Bezprzewodowe czujniki drgań są przeznaczone do pomiarów w miejscach trudno dostępnych, a tym samym podstawowym wymaganiem jest, aby na jednej baterii pracowały przez kilka lat. Jest to główna różnica pomiędzy takimi czujnikami, a innymi, codziennymi bezprzewodowymi elektrycznymi urządzeniami, których używamy (głośniki, telefony, itd.). Z tego względu, bezprzewodowe czujniki drgań są przewidziane do wielomiesięcznej pracy bez wymiany baterii. W konsekwencji, logika rejestracji sygnałów, parametry rejestrowanych sygnałów drgań oraz metody przetwarzania sygnałów drgań są mocno ograniczone względem układów przewodowych zasilanych z sieci, co pokazano schematycznie na Rysunku 2 w zestawieniu z możliwościami lokalizacji czujników obu typów.
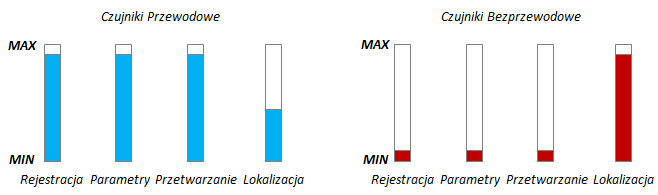
Rysunek 2 Porównanie wybranych aspektów czujników przewodowych i bezprzewodowych
Poniżej omówione są szczegóły wymienionych ograniczeń.
Logika rejestracji
W przeciwieństwie do systemów monitorowania ciągłego, czujniki bezprzewodowe wybudzają się raz na jakiś czas, zbierają dane, przetwarzają je, po czym znowu przechodzą w stan uśpienia. Typowo, wybudzanie przebiega synchronicznie, np. raz na 8 godzin. W systemach zaawansowanych (np. AVS 2000R) możliwe jest zwiększenie częstości rejestracji wraz ze wzrostem poziomów sygnałów drgań, jak pokazano na Rysunku 3.
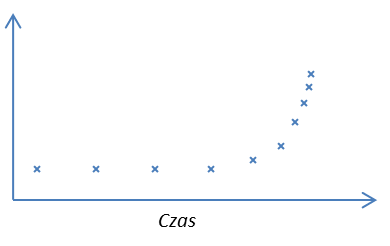
Rysunek 3 Zależność częstości rejestracji od poziomu drgań
Dynamiczna rejestracja przedstawiona na Rysunku 3 z jednej strony ogranicza zużycie baterii kiedy „nic się nie dzieje”, a skupia się na dokładniejszym pomiarze, kiedy uszkodzenie się rozwija.
Parametry sygnałów drgań
Najistotniejsze parametry akwizycji sygnałów drgań to długość sygnału i częstotliwość próbkowania. W typowych systemach CMS, rejestrowane sygnały mają długość od 1s do 10s. Co do zasady, im wolniej obraca się maszyna, tym rejestrowany sygnał powinien być dłuższy. Jeśli monitorowane zorientowane jest na detekcję niewyrównoważenia, rozosiowania, bądź ogólny poziom drgań wg. ISO 20816, wtedy częstotliwość próbkowania 2kHz może wystarczyć. Z drugiej strony, jeśli system oceny stanu technicznego ma służyć wczesnemu wykrywaniu uszkodzeń łożysk tocznych, bądź innych zjawisk wzbudzających drgania strukturalne, wtedy wymagana jest częstotliwość próbkowania rzędu 20 kHz albo więcej. W rezultacie, dla podanych wartości przedziałów długości sygnału oraz przedziałów częstotliwości próbkowania, liczba próbek w buforze wynosi od 2 tysięcy (1 s * 2000 próbek/s) do 200 tysięcy (10 s * 20000 próbek/s).
Dla obecnie istniejących czujników bezprzewodowych, podana górna granica ilości próbek jest praktycznie nieosiągalna, przede wszystkim z uwagi na ograniczenia mocy procesora i rozmiaru pamięci. Z uwagi na dostępne biblioteki obliczeniowe (np. FFT), czujniki bezprzewodowe często korzystają z buforów 2^n próbek do dalszych obliczeń. Dla tej wartości, czujnik może zbierać np. 1-sekundowy sygnał z częstotliwością próbkowania fs = 2048 Hz (2048 próbek) albo sygnał o długości L = 0.125 s z częstotliwością próbkowania fs = 16384 Hz (również 2048 próbek). W pierwszym przypadku, rozdzielczość widmowa wynosi 1 Hz, a w drugim aż 8 Hz. W obliczeniach posługujemy się zależnościami:
Ilość_próbek = L * fs
Rozdzielczość = 1 / L = fs / Ilość_próbek
Ilustrację graficzną omówionych zależności przedstawiono na Rysunku 4. Należy dodatkowo pamiętać, że drania mierzone przez akcelerometry (tj. drgania bezwzględne) są obarczone dość dużą wariancją komponentów losowych (czyli są zaszumione), dlatego ogólnie zaleca się wielokrotne uśrednianie rejestrowanych cykli. W praktyce oznacza to, że dobrze jest, gdy przetwarzany sygnał drgań zawiera przynajmniej kilka okresów analizowanych komponentów. Np. sygnały o długości 1s są odpowiednie do analizy wałów obracających się z prędkością min. 600 RPM (czyli min. 10 Hz).
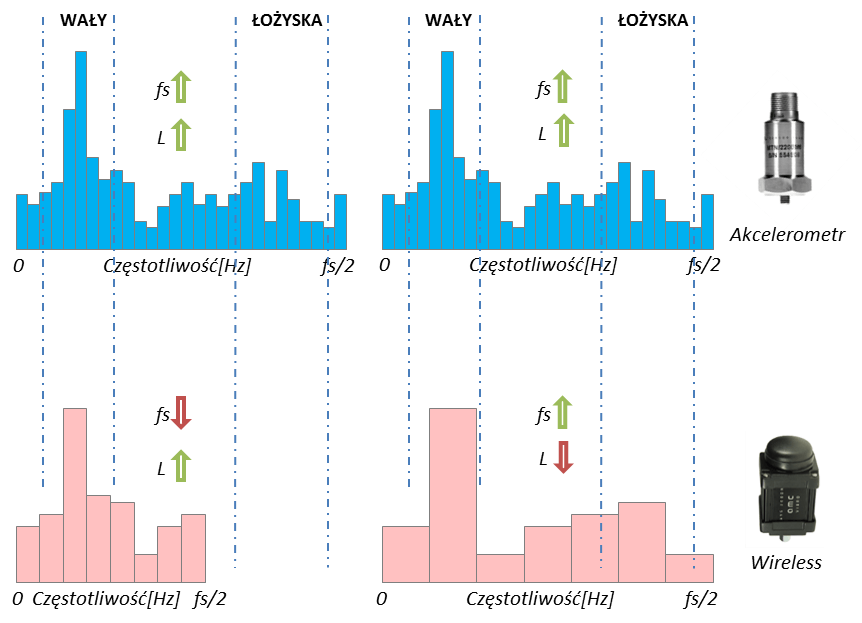
Rysunek 4 Parametry akwizycji i ich wpływ na rozdzielczość i zakres widmowy
Jak wynika z Rysunku 4, ustawienia parametrów rejestracji sygnałów dla czujników bezprzewodowych sprowadzają się do wyboru pomiędzy większym zakresem częstotliwościowym (większy zbiór wykrywanych uszkodzeń) a lepszą rozdzielczością widmową (dokładniejsza identyfikacja uszkodzeń generujących komponenty niskoczęstotliwościowe – głównie wały napędowe).
Metody przetwarzania sygnałów
Z uwagi na swoją charakterystykę, czujniki bezprzewodowe nie mierzą fazy sygnałów (tj. nie mierzą chwilowej prędkości obrotowej maszyny), w związku z czym nie wykonują analizy w dziedzinie rzędów. Z praktycznego punktu widzenia oznacza to, że są przeznaczone do ciągłego monitorowania maszyn pracujących w stałych warunkach operacyjnych. W ślad za ograniczonym przeznaczeniem czujników bezprzewodowych oraz ograniczonymi możliwościami w zakresie akwizycji sygnałów idą ograniczenia metod przetwarzania sygnałów, które mogą być zaimplementowane na takich czujnikach. Typowe czujniki bezprzewodowe mierzą następujące wartości:
- PP Acceleration – wartość międzyszczytowa (z ang. Peak-Peak) sygnału przyspieszenia drgań
- RMS Acceleration – wartość skuteczna sygnału przyspieszenia drgań
- RMS Velocity – wartość skuteczna sygnału prędkości drgań (w tym wg ISO20816)
- PP Envelope – wartość międzyszczytowa sygnału obwiedni przyspieszenia drgań
- RMS Envelope – wartość skuteczna sygnału obwiedni przyspieszenia drgań
Łatwo zatem wywnioskować, że lista obliczanych wskaźników diagnostycznych dla czujników bezprzewodowych jest znacznie uboższa niż dla czujników przewodowych i typowo ogranicza się do klasycznych wartości szerokopasmowych. Systemy bardziej zaawansowane, takie jak moduły z serii AVS 2000R, dodatkowo pozwalają definiować analizy wąskopasmowe, co umożliwia identyfikację uszkodzonego elementu maszyny. Niektóre systemy rejestrują też temperaturę w miejscu pomiaru, co jest bardzo przydatną funkcją.
Metody obliczeniowe analiz sygnałów prędkości (VRMS) oraz sygnałów obwiedni (EnvPP, EnvRMS) są podobne do obliczeń w systemach przewodowych, jednakże ze względu na małą elastyczność w długości buforów przetwarzanych sygnałów, parametry konfiguracji analiz są dość ubogie i sprowadzają się praktycznie do wyboru częstotliwości zaporowej filtru górnoprzepustowego i dolnoprzepustowego sygnału obwiedni z ograniczonej listy. Wartość RMS sygnału prędkości (VRMS) typowo mierzona jest w zakresie 10Hz-1000Hz, zgodnie z ISO 20816 i ze względu na ograniczoną długość analizowanych sygnałów nie obejmuje maszyn z prędkością obrotową poniżej 600 RPM.
Podsumowanie
Przede wszystkim należy pamiętać, że czujniki bezprzewodowe mają swoje ściśle określone miejsce w diagnostyce maszyn technicznych. Nie należy ich stosować jako zamienników systemów przewodowych – ich miejsce jest tam, gdzie montaż kabli jest praktycznie niemożliwy albo bardzo kosztowny. Konfigurując czujniki bezprzewodowe należy oprzeć się pokusie ustawiania „wyśrubowanych” parametrów akwizycji oraz przetwarzania sygnałów, gdyż odbije się to na żywotności baterii. W stosunku do czujników przewodowych, czujniki bezprzewodowo mogą niewiele, ale przy odpowiedniej lokalizacji mogą dać bardzo dużo dla służb utrzymania ruchu. Liczba węzłów konfiguracji jest u nich uboga, niemniej jednak brak złożonej konfiguracji metod przetwarzania sygnałów niejednokrotnie stanowi zaletę dla wielu operatorów. Najlepiej sprawdzają się do zastąpienia pomiarów przenośnymi miernikami drgań, szczególnie w miejscach gdzie jest utrudniony dostęp. Takie pomiary wykonuje się co kilka dni, tygodni, a nawet miesięcy. Pomiar kilka razy na dobę daje dużo większą informację użytkownikowi.
Bezprzewodowy system AVS 2000R + AVM GATEWAY
Moduły z serii AVS 2000R to bezprzewodowe dwukanałowe, konfigurowalne urządzenia pozwalające na ciągłe monitorowanie i diagnostykę maszyn. Moduł pozwala na przesyłanie informacji na temat stanu maszyn przy pomocy sieci radiowej. Dane pomiarowe zbierane są cyklicznie zgodnie ze skonfigurowanym interwałem, a w razie problemów z komunikacją przechowywane są w wewnętrznej pamięci urządzenia i przesyłane w momencie nawiązania połączenia tak aby zachowana była ciągłość pomiarowa. Czujnik sam wyznacza parametry sygnałów drgań, dzięki czemu przesyłane jest o wiele mniej danych. Nowoczesną cechą modułu jest śledzenie drgań wybranych komponentów maszyny. | ![]() |
Głównymi funkcjami AVM GATEWAY jest zarządzanie siecią czujników oraz zbieranie i przetwarzanie danych z urządzeń. Gateway jest klientem serwera OPC oraz jest zgodny z protokołem komunikacyjnym Modbus TCP. Dzięki temu czujniki AVS2000R można szybko i łatwo zintegrować z systemami sterowania (albo SCADA). Moduł posiada również serwer www, służący do konfiguracji systemu przez użytkownika i przeglądania zebranych danych. Wystarcza do tego zwykła przeglądarka internetowa. | ![]() |